-
Manufacturing engineers on the cusp of delivering new biotherapies
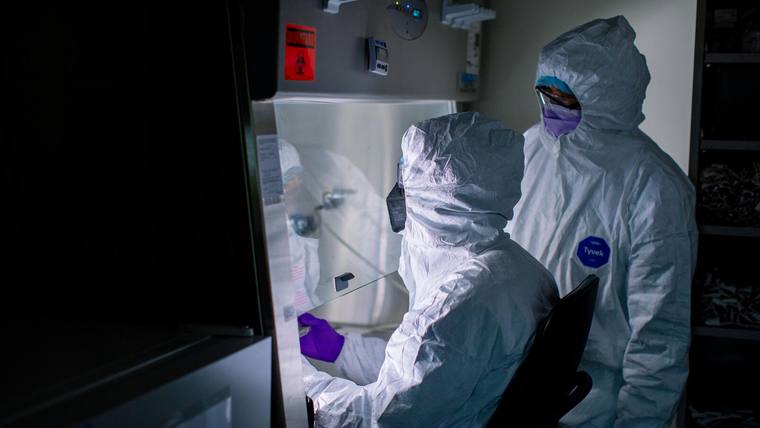
Manufacturing engineers are at the forefront of bringing new medicines derived from human sources such as cells, blood and genes to patients. They produce what are often first-of-their kind biotherapies for diseases that previously had few or no treatment options.
"The most interesting thing about our job is being able to be part of a team that brings transformative cell-based therapies to the clinic," says Kyle Ecker, advanced biomanufacturing engineer supervisor at Mayo Clinic in Florida. "It's incredibly fulfilling to understand the scientific basis of these therapies and watch them come to life by manufacturing products for individual patients."
Mayo Clinic's Center for Regenerative Biotherapeutics has 40 manufacturing engineers in Rochester and Florida. Their work makes it possible for researchers to conduct studies that require cells to be engineered on a very short timeline. In some cases, they've been able to have cells taken from patients, manufactured and returned to them in a few weeks or less. Chimeric antigen receptor (CAR-T) cell therapy for B-cell cancers and a cell-based vaccine for ovarian cancer are two examples of experimental biotherapies manufactured at Mayo Clinic.
"Our engineering teams are very dedicated to patients. They know the importance of their job, and that's to get these drugs manufactured successfully so they can be given to patients in clinical trials," says Snigdha Rai, senior director of advanced biomanufacturing in the Center for Regenerative Biotherapeutics. "Without the engineers there would be no biomanufacturing and no cell and gene therapies for patients."
Special clean room procedures
Manufacturing engineers work within a highly controlled laboratory setting or "clean room.” Clean rooms are facilities that operate according to current Good Manufacturing Practice (cGMP) regulations to ensure therapies are consistently manufactured and meet strict quality standards. These controlled environments have powerful purification systems to filter out pollutants such as dust, airborne particles, bacteria, fungus and mold that could compromise drug safety.
Adherence to strict cleanliness guidelines dictates how engineers do their job. Before stepping into a clean room, they train extensively how to operate in a cGMP facility without triggering contamination. They perform techniques to keep everything extremely clean or sterile, using high dexterity skills such as taking the cap off a vial and putting it back on with one hand, while the other hand fills it with a chemical compound.
They dress in coveralls or a "bunny suit" with a hood, goggles, face shield, double gloves and boot covers to block any escape of hair or skin cells. Once they've entered the clean room, their movements are slow and intentional.
"Rapid movements or quick opening of doors could trigger the sensors that monitor for microscopic particles," says Ecker. "People and materials must flow in a specific path to prevent any type of contamination. For example, we move in one direction, entering the clean room through one door while exiting through a separate door."
A blueprint for biomanufacturing
Manufacturing engineers have the pivotal role of being the first to run processes that transform a cell and gene therapy from a discovery into experimental medicine for use in human clinical trials. They strictly follow standard operating procedures — a blueprint of sorts — to mass produce a new therapy. A minimum of two engineers work together at all times to ensure all cells are processed according to regulatory and quality standards.
"The team works very closely each step of the way. We check each other's work and keep detailed records confirming that all procedures have been completed," says Qing Cindy Shao, Ph.D., lead advanced biomanufacturing engineer. "There is no room for error."
An important function of the job is identifying when a procedure doesn’t work as intended. The therapy is then sent back to the investigator and process development group to troubleshoot the issue and make appropriate changes. On-site manufacturing facilities make it possible to address the errors early and resolve them quickly. That helps minimize delays for patients.
"Our manufacturing engineers are indispensable. They work with quality control, quality assurance and process development to ensure the therapy meets the requirements and are safe for patients," says Alina Oancea, manager of cGMP manufacturing. "When the processes work as intended, it takes about two weeks to manufacture a CAR-T cell product."
Engineers' shifts in a clean room could range from three to 10 hours depending on the project they are working on. When they've completed their process for the day, they turn off the equipment, clean up the space and dispose of biowaste. Their work plays a central role in Center for Regenerative Biotherapeutics’ strategy of biomanufacturing new cell and gene biotherapies and collaborating with industry to make them available to patients around the world.
###
Related stories:
Ultra-clean rooms are shaping the next generation of biotherapeutics
Electrospinning biotherapies of tomorrow