-
Radiology, Engineering investigating ways to help Mayo Clinic during COVID-19 response
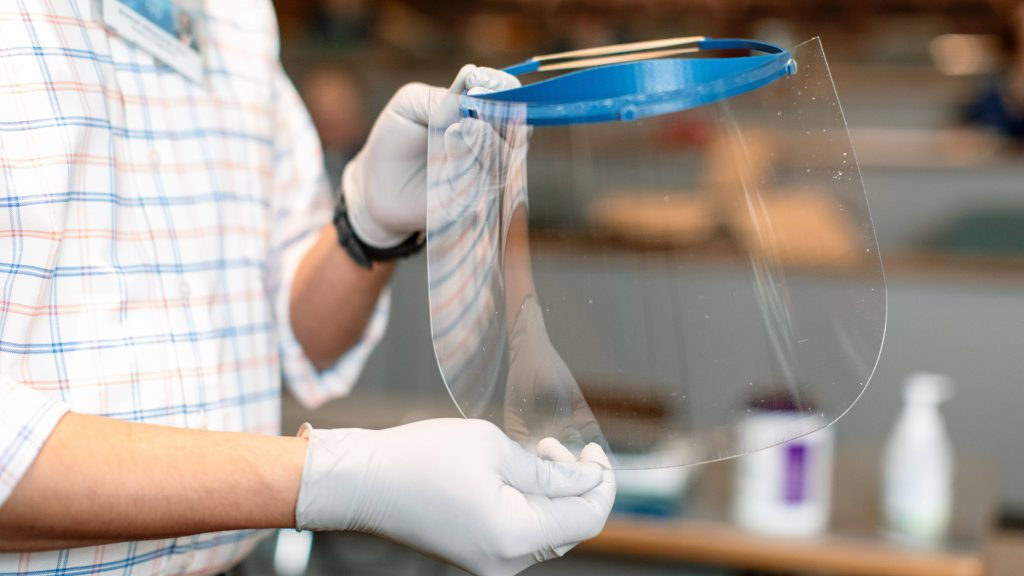
ROCHESTER, Minn. ― A supply shortage of critical materials, such as ventilators, face shields and masks, is possible in the U.S. In response, several Mayo Clinic teams have reached out to colleagues to assess their current and expected needs. These teams also are determining how they could print critical medical supplies as part of the organization's response to the COVID-19 pandemic.
3D Anatomic Modeling Laboratory locations at Mayo Clinic in Arizona, Florida and Rochester, as well as the Division of Engineering, have been discussing products that they could collaborate on to try to meet future demand.
Jonathan Morris, M.D., medical director of the 3D Anatomic Modeling Laboratory at Mayo Clinic in Rochester, says that the situation in Italy indicates what could happen in the U.S. if health care workers do not have access to the vital clinical resources needed to care for patients with COVID-19. Already some health care systems have been overloaded, and there are shortages of crucial medical supplies and equipment worldwide.
Mark Wehde, chair of the Division of Engineering, says teams across Mayo are working together to reverse-engineer, 3D-print and machine solutions for patient care.
"We are creating a command center focused on, among other projects, the work we are doing to evaluate and potentially reverse-engineer replacement ventilators," Wehde says, adding that staff from Healthcare Technology Management and the Hospital Incident Command System, both of which coordinate responses to emergency situations, and clinical areas and others will be involved in this collaborative venture. "This would be a one-stop shop for emergency engineering requests related to COVID-19 response."
Sean McEligot, unit head and director of the Additive Manufacturing Facility, which is part of the Division of Engineering, says their project managers, engineers and machinists address mechanical, electrical and software needs that arise daily across Mayo Clinic. He says they are positioned to shift gears to meet changing needs during urgent situations.
"As engineers, we can apply 3D printing and machine shop production to manufacture products that may be in limited supply," McEligot says. "For example, we have been working with Dr. Morris on a laryngoscope, which has parts that are potentially in short supply."
When called on, engineers visit with physicians and researchers to examine the products — whether they currently exist or are just sketches — and then turn them into 3D renderings that can then be 3D printed or produced in the machine shop, he says.
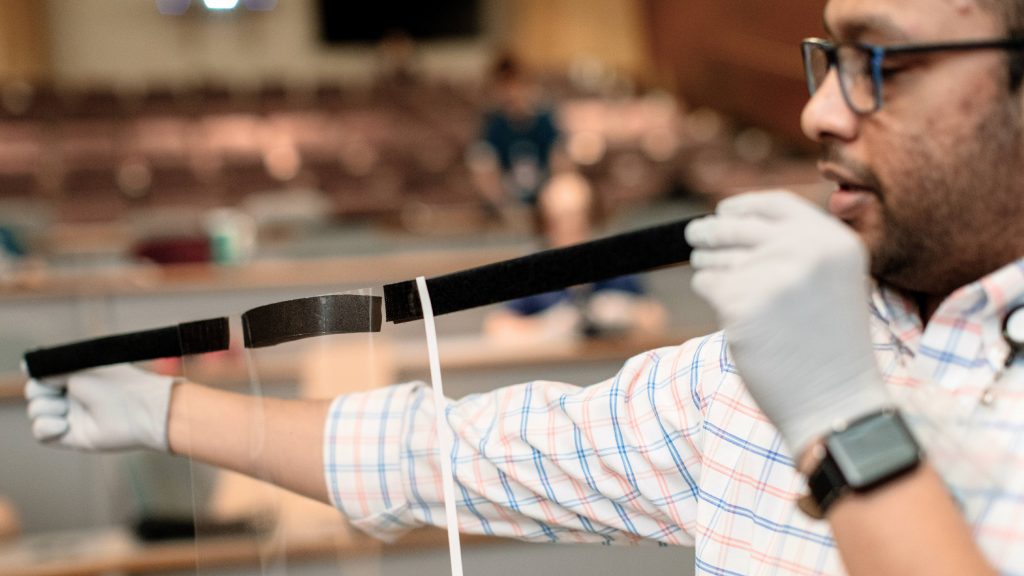
Face shields and N95 masks
Dr. Morris says his team is looking at the possibility of printing components of N95 mask equivalents or powered air-purifying respirator devices and Engineering is developing an alternative source for N95 masks, combining commercial and injection-molded parts with prototypes due within a couple of weeks.
The 3D Anatomic Modeling Laboratory locations at Mayo Clinic in Arizona and Florida are evaluating different 3D printed N95 mask designs.
"We all know how important it is to stay ahead and prevent any supply shortages we have seen around the world," Dr. Oklu says. "I've devoted my free time to this effort and look forward to helping our colleagues in whatever way I can."
"We found some open-source designs that we wanted to try out," says Robert Pooley, Ph.D., medical director of the 3D Anatomic Modeling Laboratory at Mayo Clinic in Florida. "These need to be tested to determine which designs works best, and then work through quality control processes and approvals before ramping up production to meet any clinical needs that might arise.
"But we are excited to have an opportunity to help out during this challenging time," Dr. Pooley says.
Working with the teams at Mayo Clinic in Rochester, Maarten Rotman, Ph.D., of Mayo Clinic's Office of Entrepreneurship, and Shawn Robinson, of Mayo Clinic's Life Sciences Incubator, are working to identify opportunities and solutions from Mayo Clinic in Florida and bring some unique 3D printing capabilities to the team, Wehde says.
"The cross-site collaboration and local team effort have been inspiring to say the least," Robinson says. "The Florida Simulation Center, Department of Radiology and 3D printing teams, and so many more, have contributed to the design and testing of prototype replacement masks, shields and ventilator parts that have shown to be feasible alternatives due to the potential supply shortages."
Robinson says Charles Bruce, M.D., chief innovation officer, Mayo Clinic in Florida; Amy Pollak, M.D., Cardiovascular Disease; Peter Pollak, M.D., Cardiovascular Disease; Steven Bowers, M.D., Surgery; Pablo Moreno Franco, M.D., chair of the Department of Critical Care; Michelle Freeman, M.D., Critical Care; and Abdallah El Sabbagh, M.D., Cardiovascular Disease, are among the many contributors who joined the efforts in Florida. "This entire experience has been a great example of how necessity drives performance and innovation," he says.
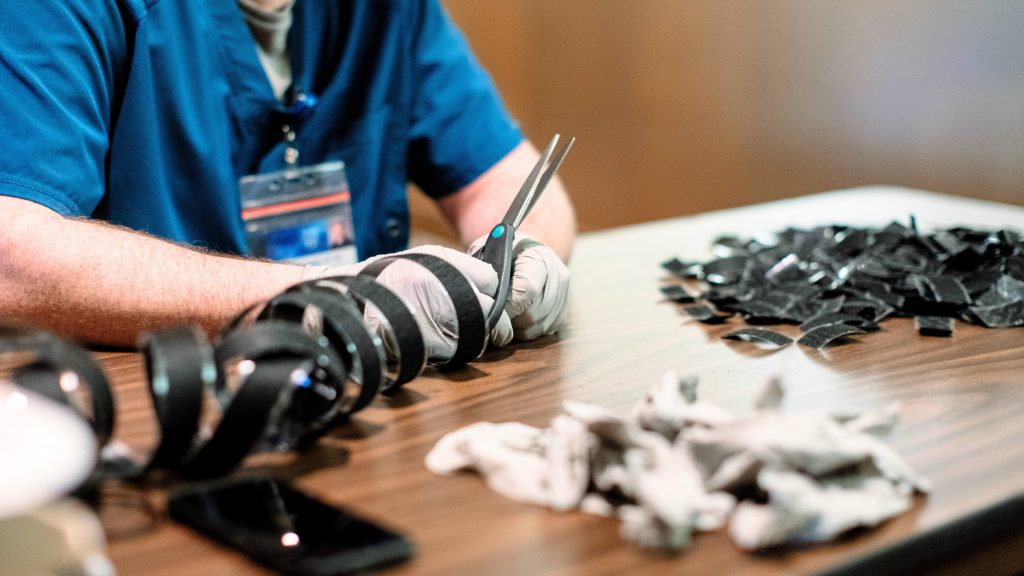
Critical supplies
McEligot adds that requests for ventilator adapters and a solution to limit the potential for cross-contamination of COVID-19 tests have come in from across Mayo.
"Along with internal Mayo team members, Life Sciences Incubator members have been instrumental with leading an open-source design team focusing on a low-cost ventilator that is feasible to manufacture at scale," Robinson says.
Dr. Morris also has been contacted by additive manufacturing companies who want to know how they can work with hospitals to prevent shortages of vital equipment. Additive manufacturing is a production process in which objects are built layer by layer, as with 3D printing. Dr. Morris says that he hopes they will be able to print pieces for ventilators to meet growing demand.
"Mayo Clinic is preparing for many scenarios, and the 3D Anatomic Modeling Labs can be part of these efforts," Dr. Morris says. "We have one of the leading point-of-care printing facilities in the world. We're willing to help in whatever way we can to manufacture products on-site. And our 3D printing peers are willing to ramp up production to meet the growing demand once they know what would be useful to produce."
Complementary efforts
In addition to these efforts, the 3D Anatomic Modeling Laboratory in Rochester also printed 3D models of SARS-CoV-2, the virus that causes COVID-19. The labs in Arizona and Rochester have 3D printed hands-free door openers for use around Mayo Clinic to limit staff contact with door handles. And the lab in Florida is working on doing the same.
Rahmi Oklu, M.D., Ph.D., medical director of the 3D Anatomic Modeling Laboratory at Mayo Clinic in Arizona, has worked with Joseph Mayer, a radiology research technologist, to design a prototype for a "no-hands" door opener for use in the Department of Radiology, with hopes to expand their use around facilities at Mayo Clinic in Arizona.
###
About Mayo Clinic
Mayo Clinic is a nonprofit organization committed to innovation in clinical practice, education and research, and providing compassion, expertise and answers to everyone who needs healing. Visit the Mayo Clinic News Network for additional Mayo Clinic news and An Inside Look at Mayo Clinic for more information about Mayo.
Media contact:
- Ethan Grove, Mayo Clinic Public Affairs, newsbureau@mayo.edu